প্রাথমিক বিবরণ
শিপিং পদ্ধতি:海运, 快递, 空运, 陆运
পণ্যের বিবরণ
Inflatable Mold for Beams/Inflatable Mold for Beams is a temporary mold tool widely used in construction engineering, bridge construction, pipeline manufacturing and other fields. It is mainly used to form the inner mold of the hollow structure when pouring concrete. The following is a detailed introduction to the inflatable core mold:
1. Working principle of the inflatable core mold
The core mold made of flexible material is expanded and formed by inflation (usually using compressed air) and filled in the position where the cavity needs to be reserved. After the concrete solidifies, the air is deflated and the core mold is removed to finally form the designed hollow structure.
2. Main application scenarios
Bridge construction: used for the internal cavity molding of prefabricated box beams and hollow bridge piers.
Building components: such as hollow slabs, columns, domes, etc.
Pipeline manufacturing: molding of concrete culverts and drainage pipes.
Water conservancy projects: casting of hollow structures such as gates and aqueducts.
3. Materials and structures
Material: high-strength rubber (such as natural rubber, chloroprene rubber) or PVC-coated fabric, with wear-resistant and pressure-resistant properties.
Structure: usually cylindrical, square or special-shaped design, with smooth surface to reduce adhesion with concrete.
4. Usage process
Installation and fixation: Place the uninflated core mold in the steel frame and fix the position.
Inflation and pressurization: Use an air pump to inflate to the specified pressure (usually 0.02-0.05MPa), and check whether it expands evenly.
Pouring concrete: Pour in layers and vibrate to avoid direct impact on the core mold.
Deflation and removal: Deflate the concrete after initial setting, and pull out the core mold for cleaning and standby.
5. Advantages and precautions
Advantages:
Lightweight and flexible: light weight, easy to carry and install, suitable for complex shapes.
Cost saving: no need to disassemble the hard formwork, saving labor and materials.
Efficient molding: shorten the construction period, especially for batch prefabricated components.
Precautions:
Air pressure control: insufficient inflation is easy to deform, excessive inflation may burst, and the pressure needs to be strictly monitored.
Protective measures: Avoid steel bars scratching the core mold, and use protective layer pads during pouring.
Temperature influence: Heat-resistant materials need to be selected in high temperature environments, and low temperatures may affect rubber elasticity.
6. Common problems and solutions
Leakage: Perform air tightness test before use, and repair damage in time (special rubber glue).
Adhesion concrete: The surface of the core mold can be coated with a release agent (such as talcum powder, special release oil).
Displacement and deformation: Add fixed straps to control the pouring speed.
7. Selection suggestions
Bridge construction: used for the internal cavity molding of prefabricated box beams and hollow bridge piers.
Building components: such as hollow slabs, columns, domes, etc.
Pipeline manufacturing: molding of concrete culverts and drainage pipes.
Water conservancy projects: casting of hollow structures such as gates and aqueducts.
3. Materials and structures
Material: high-strength rubber (such as natural rubber, chloroprene rubber) or PVC-coated fabric, with wear-resistant and pressure-resistant properties.
Structure: usually cylindrical, square or special-shaped design, with smooth surface to reduce adhesion with concrete.
4. Usage process
Installation and fixation: Place the uninflated core mold in the steel frame and fix the position.
Inflation and pressurization: Use an air pump to inflate to the specified pressure (usually 0.02-0.05MPa), and check whether it expands evenly.
Pouring concrete: Pour in layers and vibrate to avoid direct impact on the core mold.
Deflation and removal: Deflate the concrete after initial setting, and pull out the core mold for cleaning and standby.
5. Advantages and precautions
Advantages:
Lightweight and flexible: light weight, easy to carry and install, suitable for complex shapes.
Cost saving: no need to disassemble the hard formwork, saving labor and materials.
Efficient molding: shorten the construction period, especially for batch prefabricated components.
Precautions:
Air pressure control: insufficient inflation is easy to deform, excessive inflation may burst, and the pressure needs to be strictly monitored.
Protective measures: Avoid steel bars scratching the core mold, and use protective layer pads during pouring.
Temperature influence: Heat-resistant materials need to be selected in high temperature environments, and low temperatures may affect rubber elasticity.
6. Common problems and solutions
Leakage: Perform air tightness test before use, and repair damage in time (special rubber glue).
Adhesion concrete: The surface of the core mold can be coated with a release agent (such as talcum powder, special release oil).
Displacement and deformation: Add fixed straps to control the pouring speed.
7. Selection suggestions
Choose size, shape and material according to project requirements, and special-shaped structures need to be customized. It is recommended to choose brand products to ensure compressive strength and durability.
If you have specific application scenarios or operational questions, you can provide more details and I can answer further! 😊
পণ্যের বিবরণ
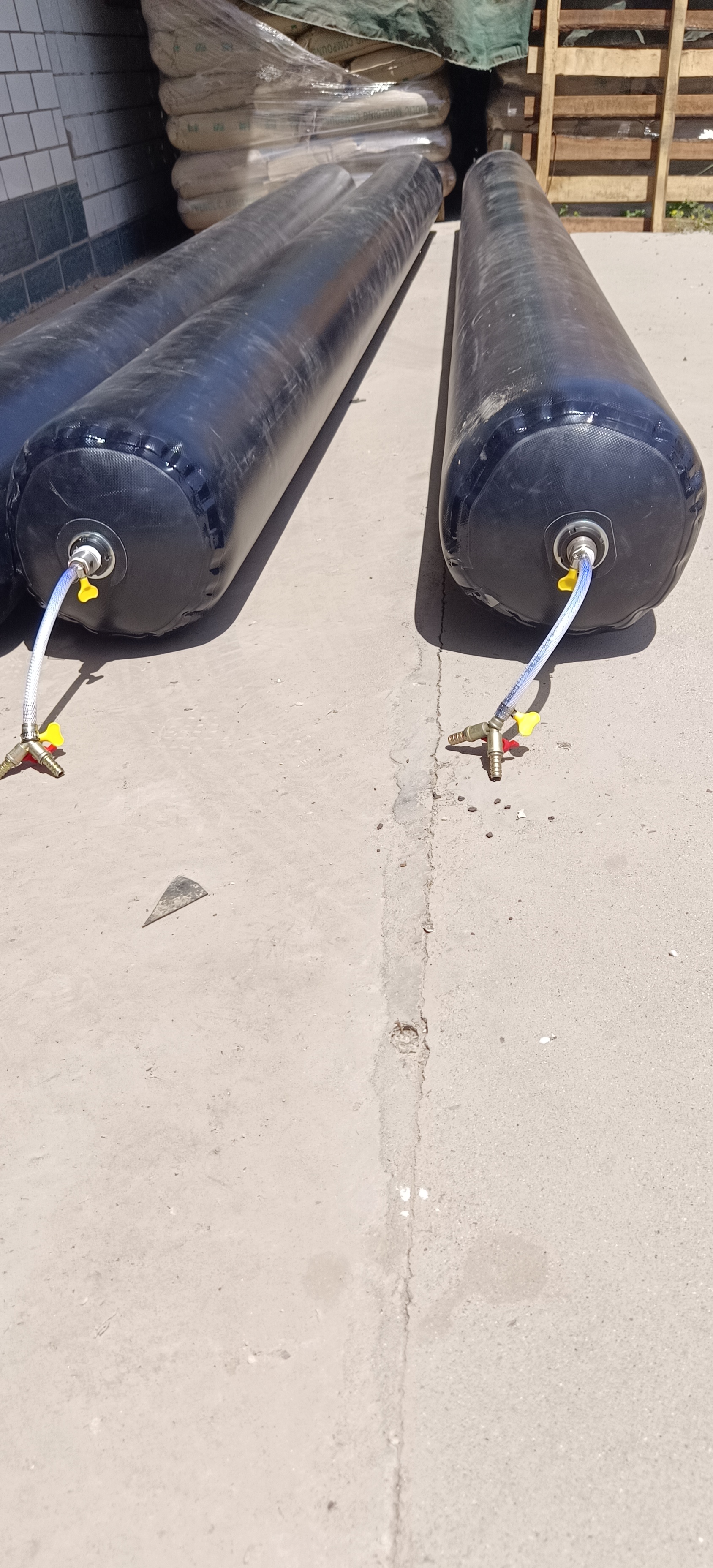